西南地区某国有企业紧固件生产车间从传统生产模式迈向精益智造的精彩篇章。通过引入15台V15F‘小举人’叉车AGV与智能调度系统,该车间成功打通冷镦、热锻、热处理等核心产线的物流脉络,实现全流程物料高效流转,成为行业智能化转型的典范。
客户需求
随着市场竞争加剧,传统紧固件生产车间的物流模式逐渐暴露出人工作业效率低、劳动强度大;不同产线间物料流转缺乏统一调度,常出现转运延迟、路径冲突等问题。此外,企业缺乏对生产物流数据的实时监控与分析手段,无法精准掌握生产进度和物料状态,难以实现精益化管理。该企业迫切需要一套智能化物流解决方案,提升物流效率、降低运营成本、保障生产安全,并通过数据驱动优化生产决策。
解决方案
根据现场勘察和交流,艾吉威机器人为该国有企业规划的智能物流解决方案包括:
1、硬件层面15台V15F叉车AGV
引入15台V15F‘小举人’叉车AGV,这些 AGV 具备强大的负载能力和精准定位功能,能够适应车间复杂的作业环境,承担冷镦产线、热锻产线、热处理产线间半成品的上料、下料以及成品的入库出库任务。
2、软件层面,部署智能调度系统
该系统犹如物流中枢大脑,通过先进的算法对多台 AGV 进行任务分配和路径规划。系统实时收集 AGV 的位置、任务状态等信息,动态调整作业计划,避免 AGV 之间的路径冲突,实现高效协同作业。同时,将智能调度系统与车间的 MES 系统深度融合,打通生产与物流的数据壁垒。MES 系统实时监控生产进度和物料需求,将相关指令传输给智能调度系统,后者据此调配 AGV 执行物料转运任务;AGV 在作业过程中产生的数据,如物料流转时间、设备运行状态等,又反馈至 MES 系统,为生产数据分析和决策提供支持。
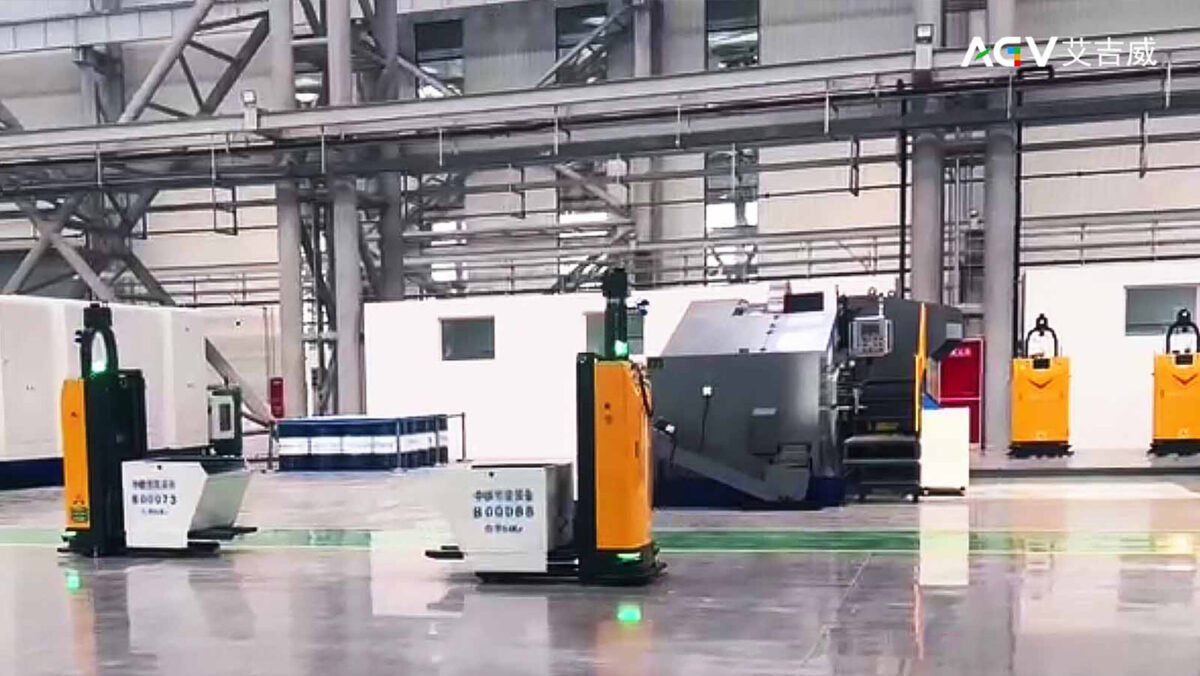
项目难点
1、空间规划难题
车间内部空间布局紧凑,既有固定的生产设备,又有频繁往来的人员,规划AGV安全高效的运行路径,避免与人员、设备发生碰撞难度大。
2、调度算法挑战
不同产线的生产节奏存在差异,冷镦、热锻、热处理等工序对物料的需求时间和数量各不相同,智能调度系统需精准匹配各产线需求,对调度算法的复杂性和灵活性要求极高。
3、系统对接困境
将智能调度系统与现有的 MES 系统进行对接,涉及不同系统的数据格式转换、接口开发和兼容性调试,易出现数据交互不畅、系统不稳定等问题。
效益体现
1、效率提升
智能调度系统的指挥下,实现了物料的快速、精准转运,物流效率提升了 30%,有效减少了生产线的停工等待时间,提高了整体生产效率。
2、成本降低
因人为操作导致的物料损耗显著降低,AGV的精准作业避免了物料在搬运过程中的磕碰、掉落等情况,物料损耗率下降20%,直接降低了生产成本。
3、安全保障
AGV 配备的多种安全防护装置,如激光雷达、防撞触边等,能够及时感知周围环境,在遇到障碍物时自动停止,大大减少了叉车碰撞、货物倾倒等安全事故的发生概率。
4、智能管理
通过与 MES 系统的协同,企业实现了生产数据的实时监控与分析。管理人员能够随时掌握物料流转情况、设备运行状态、生产进度等信息,为生产计划制定、资源调配提供了准确的数据依据,推动企业生产管理向智能化、精益化方向迈进。